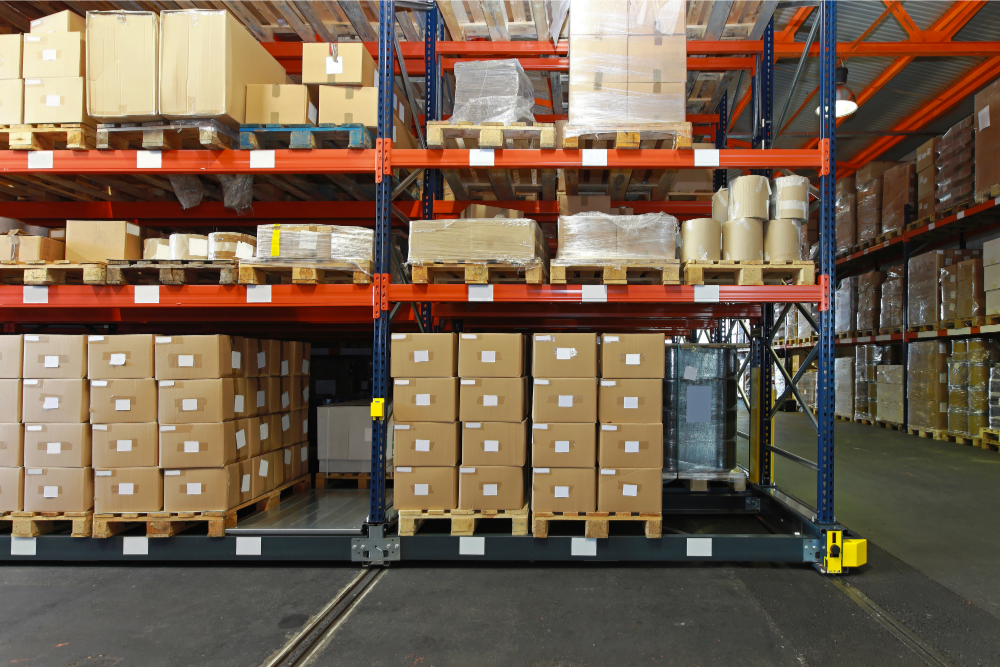
物流倉庫を効率的に稼働させるためには、レイアウトが非常に重要です。最適なレイアウトが実現すると、コスト削減や出荷リードタイムの短縮化、事故防止といったメリットがあるので、競争優位に立つためのポジティブな要因となりえるでしょう。そこで今回は、物流倉庫のレイアウトやレイアウトを決める際の考え方について解説します。
目次
物流倉庫のレイアウトとは
物流倉庫におけるレイアウトとは、倉庫の規模や業務内容を考慮して荷主から預かる荷物の保管場所や保管方法を決めることを意味します。厳密には、物流作業で使用するフォークリフトや自動搬送機といったマテハン機器をはじめとするその他の備品を保管するスペースも合わせて最適な配置を決定する必要があるでしょう。適切なレイアウトを実現すると、以下の3つのメリットが得られます。
- コスト削減
- 出荷スピードの短縮
- ヒューマンエラーや事故の減少
不適切なロケーションに商品が配置されていると、ピッキングをする際の移動距離が増えます。頻繁に出し入れする商品が入出荷口から離れていると作業時間が大幅に増加する原因にもなるでしょう。これらの状況を改善できれば、人的コストが少なくて済むだけでなく、出荷するまでのリードタイムも短縮できます。
さらに作業員のが往来しやすいスペースが十分に確保されていると、作業員同士や自動走行するマテハン機器との接触といった事故も防止できます。どこに何があるかが分かりやすく表示されていれば、ピッキングを誤ったり誤出荷したりするリスクも抑えられるでしょう。誤出荷は余分なコストがかかるだけでなく、顧客に重大な損失を与え、自社の信頼を失墜する要因にもなりかねません。
これらのことを勘案すると、物流倉庫にとって適切なレイアウトを実現することは、業績アップや社会的信頼、さらに従業員の安全を守る意味でも非常に重要といえるのです。
それでは以下に、レイアウトを決めるにあたっての考え方を4つ紹介しましょう。なお考え方の1と2についてはどちらが先ということはありません。実際のことを考えると、1と2は同時に考慮しながらレイアウトの青写真を描く方が作業が進みやすいでしょう。
レイアウトの考え方1:保管方法とロケーション番号を決める
まず、どのような基準で商品を保管するのかを決めます。具体的には、「固定ロケーション」と「フリーロケーション」があります。
固定ロケーションは、品目や種類によって格納する棚を決める方法です。どこに何があるのかがはっきりするので棚入れもピッキングもしやすいのが特徴です。ただし、スペースが空いていても他の商品を格納できないので無駄が生じるデメリットがあります。
一方のフリーロケーションは、空いている棚に商品を格納するやり方です。棚入れはしやすいものの、どこに何があるかが分かりにくく、ピッキングに時間がかかる可能性があるのが難点です。
いずれにしても全ての棚に共通のロケーション番号(通称:ロケ番)を設定するのが有効です。例えば「Gエリアの3番通路の2番目の棚の4番間口」なら「G-03-02-04」と表示します。すると格納場所が住所のように特定できるので作業が捗りやすくなります。
レイアウトの考え方2:動線を重視する
「考え方1」と並行して、作業員の移動距離が極力短く、効率的に棚入れやピッキングができるように動線を確保することが大切です。つい棚の数を多くして格納できる在庫数を増やしたくなりがちです。しかし数量を重視するとどうしても通路が狭くなり、作業員やロボットが通りづらくなる恐れがあるので注意が必要です。
また作業員が行ったり来たりを何度も繰り返さずに済むよう、動線を確保することも重要です。もし入荷口と逆の位置に出荷口があるなら、入荷→棚入れ→ピッキング・流通加工→梱包→出荷という一連の流れが途切れずに連続でできるように、手前から奥へと直線ルートで各スペースを配置するとよいでしょう。
一方、入荷口と出荷口が同方向にある場合なら、入荷〜出荷までのルートは、手前から奥にかけて直線ルートで進み、途中でUターンして出庫口に至るように配置すると、行ったり来たりがなくせるので作業が効率化できるでしょう。
【関連記事】
物流倉庫の役割とは?仕事内容をステップごとに詳しく解説
レイアウトの考え方3:商品ごとの出荷頻度を重視する
商品の格納場所は、種類やカテゴリーごとよりも出荷頻度の多寡で分類する方が作業が効率化できます。
例えば、「歯磨き粉」と「口腔洗浄機」を取り扱っていると仮定しましょう。日常的によく売れるのは歯磨き粉で、口腔洗浄機は時々しか売れないとします。この場合なら、入荷口近くに歯磨き粉を格納し、口腔洗浄機は出荷口の近くなどあまり出入りのない端のスペースに格納する方がベターです。これが逆だと、棚入れのために何度も長距離を往復したり、ピッキングの後に流通加工や梱包スペースに繰り返し持ち運んだりするのに非常に手間がかかります。
また、売れ筋商品は、メイン通路から見てできるだけ手前に格納するのもよいでしょう。通路からすぐそばにあれば作業員がピッキングするのに手間がかかりません。通路から離れた場所にあると、ピッキングのたびに何度も枝分かれした細い通路を往復しなければならないことがあるので作業時間が長くなってしまいます。
話をわかりやすくするために単純な試算をしてみます。上記の例のように歯磨き粉が売れ筋と仮定し、メイン通路に最も近い棚に格納されているとします。そして一回のピッキングに必要な平均時間は30秒としましょう。一方、メイン通路からもっとも離れた位置に格納した場合、ピッキングしてメイン通路に戻るまでに1分かかるとします。その差は1回につき「30秒」です。
売れ筋商品のため、1日に200回のピッキングが必要と仮定すると「30秒×200回=6,000秒」。つまり、1日で「100分」の時間が短縮できる計算になります。すると、1回につき30秒で済む場合、この100分間のうちにさらに200回のピッキングができるのがわかるでしょう。また、これを1ヶ月(30日)続けると、「3,000分=50時間」の時間短縮が可能となります。1日8時間とすると、1人が6日働いた場合以上の労働時間がまるまる浮く計算になるわけです。こう考えると、出品頻度に合わせて商品の格納場所を決めることの重要性がよく理解できるのではないでしょうか。
レイアウトの考え方4:安全対策を徹底する
物流業務でもっとも注意を払わなければならないことのひとつに、作業員の安全対策があります。物流倉庫内で扱う商品には危険物や重量のかさむアイテムが含まれていることが少なくありません。それらがもし落下して作業員の体に直接触れることがあれば、甚大な被害を及ぼすおそれがあるでしょう。自動搬送機などのロボティクスとの接触事故も絶対に回避しなければなりません。
自動搬送機などには、人が近くにいることを検知すると自動的にストップする機能がついているものもあります。ただ、レイアウト上の安全対策はもっとアナログで地味なものになります。しかもそれらが意外に高い効果を生むので、決してあなどってはいけません。
代表的な対策として以下の6つが挙げられます。
- 蛍光色のガムテープで動線を区画する
- 整理整頓を徹底し動線上に余分なものを放置しない
- ヒヤリハット事例の共有と注意喚起を徹底する(ヒヤリハット=「ヒヤリ!」「ハッと!」するような危険な事象のこと)
- フォークリフトや自動搬送機の通路を限定する
- 作業員同士の声がけを徹底する
- 在庫棚を固定する
これらの基本事項を周知徹底し、決して口だけ、形だけとならないように、現場のトップ自らが高い意識をもって遵守し続けるように努めることが大切でしょう。
まとめ
物流倉庫の最適なレイアウトは、倉庫自体の規模や扱う商品、作業員の人数、マテハン機器の種類などによって違ってきます。そして完璧はありません。状況を冷静に把握・分析しながら常に最良のレイアウトにアップデートしていく姿勢が求められるでしょう。
【関連記事】
物流代行サービスは倉庫保管から始まる?
毎日大量の商品を出荷、さらにロボットとの作業で効率化を図るSTOCKCREWでも上記のような対策、心がけを徹底しています。そのため、大量の商品を安全、そして確実に、さらに低価格でのご提供を実現しています。STOCKCREWに興味が出てきましたら、どんなことでもかまいません、お気軽にご連絡・ご相談ください。